Distilling Industry Operations: Navigating OSHA Regulations for Safety and Compliance
Posted: September 18th, 2024
Authors: Brian G.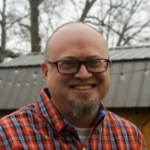
The art of distilling spirits has deep roots, blending tradition with modern technology. However, as the industry evolves, so too does the responsibility to maintain safe operations. Distilleries, like all manufacturing environments, must navigate a complex landscape of safety regulations to ensure not only quality products but also the well-being of their workers. In the United States, Occupational Safety and Health Administration (OSHA) sets the standards that distilleries must adhere to for safe working conditions.
In this post, we’ll explore how distillery operations intersect with OSHA regulations and highlight some key areas of focus for safety compliance.
Hazard Communication: A Recipe for Safe Operations
Distilleries rely heavily on chemical processes, particularly during fermentation and distillation. Ethanol, the primary product of distillation, is a highly flammable substance, requiring rigorous control and handling protocols. OSHA’s Hazard Communication Standard (HCS), also known as HazCom, mandates that all hazardous chemicals in the workplace be properly labeled and that employees receive training on how to handle them safely.
In distilleries, this means that workers need to understand:
- The dangers of ethanol vapor, which can ignite at low temperatures.
- Proper storage and labeling of hazardous materials, including cleaning agents and other solvents.
- Procedures for safely handling high-proof alcohol during bottling and transfer processes.
Process Safety Management: Preventing Explosive Hazards
The distillation process itself can be hazardous. High-pressure steam, open flames, and flammable liquids create the potential for fires and explosions. OSHA’s Process Safety Management (PSM) standard is designed to prevent catastrophic events involving highly hazardous chemicals, and while ethanol is below the threshold for mandatory PSM implementation, many distilleries opt for similar measures to ensure safe operations.
Key PSM-related activities in distilleries include:
- Conducting regular inspections of equipment, especially boilers and stills.
- Implementing strict maintenance schedules to avoid failures that could lead to accidents.
- Training employees on emergency shutdown procedures.
Machine Guarding: Protecting the Workforce
Distilleries utilize a variety of machinery, from large fermenting vats to bottling lines. OSHA’s Machine Guarding Standard ensures that workers are protected from injuries related to moving parts, such as rotating blades, conveyors, and mixers. In distilleries, machines must be equipped with appropriate safety guards to prevent entanglement, lacerations, and other injuries.
Some best practices include:
- Installing guards on bottling line machinery to protect workers from pinch points.
- Using proper ventilation systems to manage fumes and prevent the build-up of combustible gases.
- Conducting regular audits of machine safety features to ensure compliance.
Lockout/Tagout: Safeguarding During Maintenance
Maintenance is a critical component of any distillery’s operations, but it also poses risks. OSHA’s Lockout/Tagout (LOTO) Standard is designed to protect employees from the unexpected startup of machinery or the release of hazardous energy during maintenance or repair work. In a distillery, this is particularly important for equipment such as fermentation tanks, stills, and bottling lines.
LOTO procedures in distilleries typically involve:
- Shutting down and de-energizing equipment before any repair work begins.
- Applying locks and tags to prevent accidental startup.
- Training employees on how to properly implement LOTO procedures.
Confined Spaces: Safe Work in Tight Areas
Distilleries often contain confined spaces such as fermentation tanks, grain silos, or even large boilers, which pose unique risks. OSHA’s Confined Space Entry Standard requires that employers evaluate the potential hazards in confined spaces, including oxygen deficiency, toxic gases, or the potential for engulfment.
For distilleries, confined space safety includes:
- Testing the atmosphere within tanks or silos before entry to ensure safe oxygen levels.
- Using proper ventilation equipment to remove harmful vapors.
- Ensuring workers are properly trained and have emergency rescue procedures in place.
Personal Protective Equipment (PPE): A Shield Against Hazards
Distillery workers face various physical and chemical hazards. OSHA’s Personal Protective Equipment (PPE) Standards require employers to provide necessary gear to protect employees from exposure to hazardous substances, noise, and moving machinery.
In distilleries, PPE might include:
- Flame-resistant clothing (FRC) to protect against flash fires.
- Gloves and safety goggles for handling chemicals.
- Ear protection to guard against the high noise levels in bottling operations or near boilers.
- Dust Hazard Analysis: Managing Combustible Grain Dust
Grain milling and storage are essential steps in distillery operations, but they come with the significant risk of combustible dust explosions. OSHA’s Combustible Dust National Emphasis Program requires facilities that handle fine particulate materials, such as grain, to conduct a Dust Hazard Analysis (DHA). In distilleries, grain dust generated during milling, storage, and transfer can accumulate in confined areas and ignite, leading to fires or explosions.
To mitigate this risk, distilleries should:
- Regularly clean and inspect equipment to prevent dust buildup, particularly around mills, conveyors, and storage bins.
- Ensure proper ventilation systems are in place to capture dust at its source.
- Conduct DHAs to identify potential ignition sources and implement controls, such as explosion-proof electrical systems and grounding to prevent static discharge.
Electrical Safety: Powering Distillery Operations Safely
Distilleries rely on a wide range of electrical systems to power equipment, control processes, and ensure efficient operations. However, the combination of flammable materials like ethanol and grain dust with electrical systems can create significant safety hazards, including fires, explosions, and electrical shocks. OSHA’s Electrical Safety Standards are designed to mitigate these risks by enforcing strict guidelines for equipment installation, maintenance, and worker training.
Key aspects of electrical safety in distilleries include:
- Explosion-Proof Equipment
- Grounding and Bonding
- Routine Inspections and Maintenance
- Employee Training
Fall Protection: Safeguarding from Heights
In distilleries, working at heights is common, whether on catwalks, ladders, or elevated platforms for maintenance and inspections. OSHA’s Fall Protection Standard mandates the use of fall protection systems to prevent falls that could result in serious injury or death. OSHA also has requirements related to all Walking Working Surfaces that employees may encounter. This could include the use of ladders, stairways, platforms, and loading dock areas.
Key considerations for fall protection in distilleries include:
- Ensuring proper installation and use of guardrails, safety nets, or personal fall arrest systems where employees are at risk of falling.
- Regularly inspecting fall protection equipment for wear and compliance.
- Training employees on safe practices and the correct use of fall protection systems.
Emergency Preparedness: Ready for the Unexpected
Emergencies in distilleries can range from chemical spills to fires and natural disasters. OSHA’s Emergency Action Plan (EAP) Standard requires employers to develop and implement plans to address such scenarios. OSHA also addresses other emergency related items such as exit routes, fire prevention, medical emergencies, and fire protection.
Key elements of an effective emergency preparedness plan include:
- Developing and practicing emergency evacuation routes and procedures.
- Providing training on emergency response, including fire drills and chemical spill response.
- Ensuring that emergency contact information and resources are readily accessible to all employees.
Conclusion
Running a distillery requires more than mastering the craft of creating exceptional spirits. Just like a finely distilled spirit, safety in the workplace comes from careful attention to detail. It involves maintaining a safe workplace that complies with OSHA’s extensive regulations. By staying informed and compliant with OSHA regulations, distilleries can maintain a safe environment that not only safeguards workers but also contributes to a successful and sustainable business. With the right safety programs in place, distilleries can focus on what they do best—crafting quality spirits—while ensuring their workforce remains protected.
ALL4 can assist organizations with conducting internal audits, training, and by reviewing current policies and procedures. The health and safety professionals at ALL4 have extensive expertise spanning various workplace safety and health concerns. Serving a diverse array of industries, including specialty manufacturing, automotive, food and beverage, pharmaceuticals, energy, pulp and paper, and federal defense agencies, ALL4 tailors its services to meet the unique needs of each client. The ALL4 team is dedicated to developing site-specific strategies that prioritize accident and injury reduction and risk management.
For further information or to get ALL4 engaged to assist your organization, contact Brian Godfrey at 864.520.4663 or bgodfrey@all4inc.com.
OSHA Hazard Communication Standard, 29 CFR 1910.1200
OSHA Process Safety Management, 29 CFR 1910.119
OSHA Machine Guarding, 29 CFR 1910.212
OSHA Lockout/Tagout Standard, 29 CFR 1910.147
OSHA Confined Space Entry, 29 CFR 1910.146
OSHA Personal Protective Equipment, 29 CFR 1910 Subpart I
OSHA Combustible Dust National Emphasis Program, CPL 03-00-008
OSHA Electrical Safety, 29 CFR 1910 Subpart S
OSHA Fall Protection, 29 CFR 1910.28
OSHA Emergency Action Plans, 29 CFR 1910.38